Table of Contents
In the oil and gas industry, having the right equipment is essential for successful drilling operations. Each piece of equipment plays a critical role in ensuring safety, efficiency, and productivity. This article will explore the must-have oil rig equipment that every drilling operation should have, making it easier for operators to understand their importance and function.
Key Takeaways
- The derrick is crucial for lifting the drill string and supports the entire drilling process.
- Top drives are preferred over rotary tables for their efficiency and ability to drill longer sections.
- Mud pumps are essential for circulating drilling fluid, which cools the drill bit and removes cuttings.
- Blowout preventers are vital safety devices that control the release of oil and gas during drilling.
- Shale shakers help separate cuttings from drilling fluid, allowing for the reuse of the fluid and reducing costs.
Understanding the Role of the Derrick
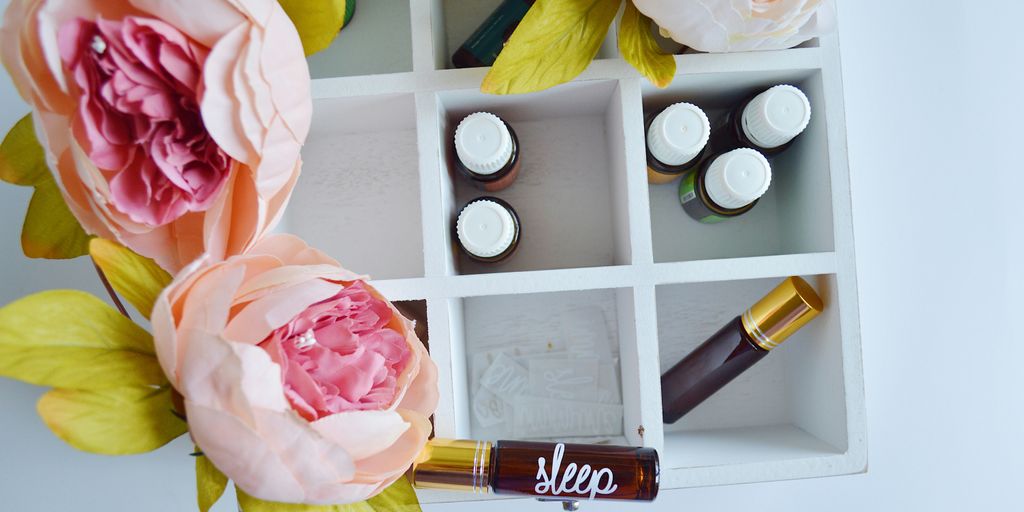
The derrick is a crucial structure in any drilling operation. It serves as the backbone of the drilling rig, providing the necessary support for the drill string and other equipment. Without a derrick, lifting and lowering the drill string would be nearly impossible, making it an essential component of the drilling process.
Importance of the Derrick in Drilling Operations
- Support Structure: The derrick holds the drill string in place and allows for its movement.
- Lifting Mechanism: It enables the lifting of heavy equipment and tools needed for drilling.
- Safety Features: Derricks are designed with safety in mind, ensuring that operations can be conducted without risk of collapse.
How the Derrick Supports the Drill String
The derrick supports the drill string through a series of components:
- Crown Block: A set of pulleys at the top of the derrick that helps in lifting the drill string.
- Traveling Block: Moves up and down the derrick, connected to the drill string.
- Drilling Line: A strong cable that connects the blocks and allows for the lifting and lowering of the drill string.
Maintenance and Safety Considerations for Derricks
Regular maintenance of the derrick is vital to ensure safety and efficiency:
- Routine Inspections: Check for wear and tear on cables and pulleys.
- Lubrication: Keep moving parts well-lubricated to prevent friction and wear.
- Load Testing: Periodically test the derrick’s load capacity to ensure it can handle the required weight.
Maintaining the derrick is not just about efficiency; it’s about ensuring the safety of all personnel involved in drilling operations.
In summary, the derrick plays a vital role in drilling operations, supporting the drill string and ensuring that the entire process runs smoothly and safely. Understanding its functions and maintenance needs is essential for any drilling operation.
The Functionality of Top Drives
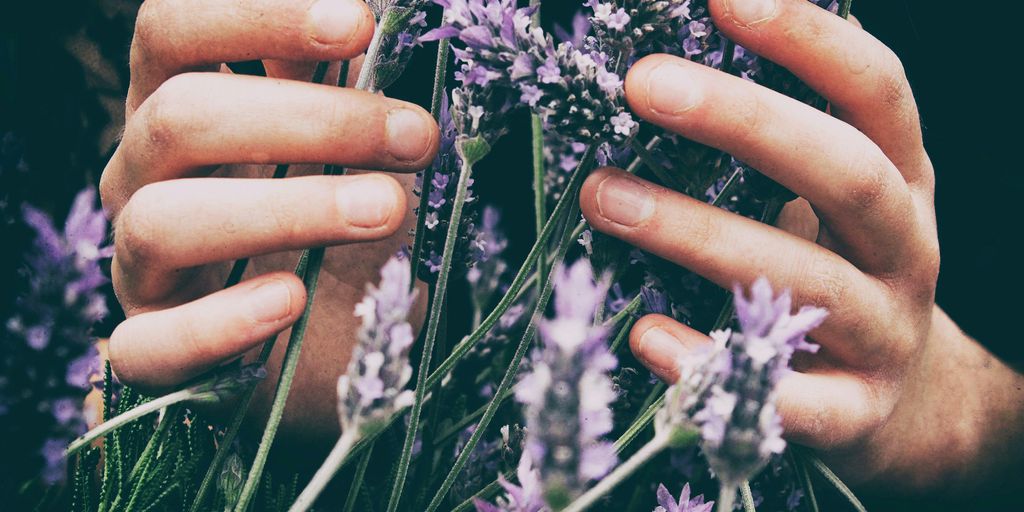
Advantages of Using Top Drives Over Rotary Tables
Top drives are a modern solution in drilling operations, offering several benefits compared to traditional rotary tables. One major advantage is their ability to drill deeper and faster. Here are some key points:
- Increased Efficiency: Top drives allow for continuous rotation, which means less downtime.
- Better Control: They provide improved torque control, making it easier to manage the drilling process.
- Reduced Wear: With less mechanical wear, top drives can lead to lower maintenance costs.
Installation and Operation of Top Drives
Installing a top drive involves several steps:
- Mounting: The top drive is mounted on the derrick above the rotary table.
- Connection: It connects to the drill string, allowing for rotation and weight application.
- Testing: After installation, thorough testing is essential to ensure proper operation.
Troubleshooting Common Top Drive Issues
Even with advanced technology, issues can arise. Here are some common problems and their solutions:
- Power Failures: Check electrical connections and backup systems.
- Torque Issues: Inspect for wear in the drive components.
- Fluid Leaks: Regularly check seals and connections to prevent leaks.
Top drives are essential for modern drilling operations, enhancing efficiency and safety. Their role in drilling cannot be overstated, as they are vital for achieving optimal performance in the field.
In summary, top drives are a crucial part of drilling equipment, providing significant advantages over older systems. Their installation and operation require careful attention, and being aware of common issues can help maintain smooth operations. Understanding these aspects is key to ensuring efficient drilling processes in the oil field.
Mud Pumps and Circulation Systems
Components of a Mud Circulation System
A mud circulation system is essential for any drilling operation. It consists of several key components:
- Mud Pumps: These are responsible for moving the drilling fluid, or mud, from the surface to the drill bit and back again.
- Mud Tanks: These store the drilling fluid and allow for its circulation.
- Shale Shakers: They separate cuttings from the mud, ensuring that the fluid remains effective.
Role of Mud Pumps in Drilling Efficiency
Mud pumps play a critical role in drilling efficiency. They ensure that the drilling fluid is continuously circulated, which helps to cool the drill bit and remove cuttings from the wellbore. This process is vital for maintaining optimal drilling conditions and preventing equipment damage.
Maintaining and Troubleshooting Mud Pumps
To keep mud pumps running smoothly, regular maintenance is necessary. Here are some tips:
- Check for leaks: Regularly inspect the pump for any signs of fluid leaks.
- Monitor pressure: Ensure that the pressure readings are within the recommended range.
- Clean filters: Keep the filters clean to prevent blockages that can hinder performance.
Regular maintenance of mud pumps is crucial for preventing costly downtime and ensuring efficient drilling operations.
By understanding the components and functions of mud pumps and circulation systems, drilling operations can enhance their efficiency and safety.
The Critical Role of Blowout Preventers
Blowout preventers (BOPs) are crucial safety devices used in drilling operations. Their primary function is to prevent the escape of pressurized fluids from the well. This is essential because uncontrolled pressure can lead to dangerous blowouts, which can cause significant damage and risk to personnel.
Types of Blowout Preventers and Their Uses
There are two main types of blowout preventers:
- Ram BOPs: These use hydraulic rams to seal the well and can handle high pressures.
- Annular BOPs: These create a seal around the drill pipe and can accommodate varying pipe sizes.
Installation and Maintenance of Blowout Preventers
Proper installation and regular maintenance of BOPs are vital for safety. Here are some key steps:
- Ensure the BOP is correctly aligned with the wellhead.
- Regularly check hydraulic systems for leaks.
- Conduct routine pressure tests to ensure functionality.
Safety Protocols Involving Blowout Preventers
To ensure safety during drilling operations, follow these protocols:
- Always have a trained crew on standby for emergencies.
- Conduct regular drills to prepare for blowout scenarios.
- Keep communication lines open between the drilling team and safety personnel.
In summary, blowout preventers are essential for controlling well pressure and ensuring the safety of drilling operations. Their proper use and maintenance can prevent catastrophic incidents and protect both workers and the environment.
Shale Shakers and Solids Control
How Shale Shakers Work in Drilling Operations
Shale shakers are essential pieces of equipment in drilling operations. They help separate the cuttings from the drilling fluid by using a vibrating screen. This process allows the fluid to flow back into the well for reuse, which is not only efficient but also saves money by reducing disposal costs.
Benefits of Effective Solids Control
Effective solids control is crucial for maintaining drilling efficiency. Here are some key benefits:
- Cost Savings: Reusing drilling fluid cuts down on disposal fees.
- Improved Performance: Clean drilling fluid enhances the drilling process.
- Environmental Protection: Reduces waste and minimizes environmental impact.
Upgrading and Maintaining Shale Shakers
To ensure optimal performance, regular maintenance and upgrades are necessary. Here are some tips:
- Regular Inspections: Check for wear and tear on screens and components.
- Timely Replacements: Replace worn-out parts to maintain efficiency.
- Upgrade Technology: Consider newer models for better performance.
Maintaining shale shakers is vital for the overall success of drilling operations. Proper care can lead to longer equipment life and better drilling outcomes.
In summary, shale shakers play a critical role in drilling operations by ensuring that the drilling fluid remains effective and cost-efficient. Their maintenance and upgrades are essential for smooth operations and cost-effective drilling.
Power Systems in Oil Rig Equipment
Power systems are the backbone of any drilling operation, providing the necessary energy to keep everything running smoothly. Without a reliable power source, drilling activities would come to a halt.
Types of Power Systems Used in Oil Rigs
- Diesel Engines: These are commonly used for their reliability and power.
- Electric Motors: Often used for mechanical subsystems, they provide efficient energy use.
- Generators: Essential for producing electricity for lighting and other electrical needs on the rig.
Ensuring Efficient Energy Use in Drilling Operations
To maximize efficiency, consider the following:
- Regular maintenance of engines and generators.
- Monitoring energy consumption to identify areas for improvement.
- Implementing energy-saving technologies where possible.
Troubleshooting Power System Failures
When issues arise, follow these steps:
- Identify the problem: Check for any obvious signs of failure.
- Consult manuals: Refer to equipment manuals for troubleshooting tips.
- Seek professional help: If the issue persists, contact a technician.
Efficient power systems are crucial for the success of drilling operations. They not only ensure that equipment runs smoothly but also enhance overall safety and productivity.
In summary, understanding the power systems in oil rigs is essential for maintaining operational efficiency and safety. Proper management and troubleshooting can prevent costly downtime and ensure a successful drilling operation.
The Importance of Drill Bits and Drill Strings
Drill bits and drill strings are essential components in any drilling operation. They play a crucial role in reaching oil and gas reserves deep underground.
Different Types of Drill Bits and Their Applications
There are several types of drill bits, each designed for specific tasks:
- Roller Cone Bits: Great for hard rock formations.
- PDC Bits: Ideal for soft to medium formations, offering faster drilling speeds.
- Diamond Bits: Used for extremely hard materials, providing durability and efficiency.
Understanding the Drill String Components
The drill string is made up of various parts that work together:
- Drill Pipe: Transmits drilling fluid and torque to the bit.
- Drill Collar: Adds weight to the drill bit, helping it penetrate harder rock.
- Kelly: Connects the drill pipe to the rotary system, allowing for rotation.
Maintaining Drill Bits and Strings for Longevity
To ensure the longevity of drill bits and strings, consider these maintenance tips:
- Regularly inspect for wear and tear.
- Keep them clean and free from debris.
- Store them properly when not in use.
Maintaining your drill bits and strings is vital for efficient drilling operations. Proper care can save time and costs in the long run.
In summary, understanding the importance of drill bits and drill strings is key to successful drilling operations. They are the backbone of any drilling project, ensuring that the process is efficient and effective. By focusing on maintenance and the right selection of tools, operators can enhance their drilling performance and achieve better results.
Conclusion
In summary, having the right equipment is crucial for any oil drilling operation. The tools we’ve discussed, like the blowout preventer, degassers, shale shakers, and mud pumps, are essential for ensuring safety and efficiency. Each piece of equipment plays a unique role in the drilling process, helping to manage pressure, separate materials, and circulate fluids. By understanding and utilizing these key components, drilling teams can work more effectively and minimize risks. Remember, investing in quality equipment not only enhances performance but also contributes to a safer working environment.
Frequently Asked Questions
What is the main purpose of a derrick in drilling?
A derrick is a tall structure that helps lift the drill string during drilling operations. It is essential for supporting the drilling process.
How does a top drive improve drilling efficiency?
A top drive is a motor that turns the drill string from above, allowing for faster and more effective drilling compared to traditional methods.
What role do mud pumps play in drilling?
Mud pumps circulate drilling fluid, which cools the drill bit and carries rock cuttings back to the surface, making the drilling process more efficient.
Why are blowout preventers important?
Blowout preventers are safety devices that control the release of oil and gas from a well, preventing dangerous blowouts during drilling.
How do shale shakers help in drilling operations?
Shale shakers separate solid materials from drilling fluid, allowing the fluid to be reused and saving costs in the drilling process.
What types of power systems are used in oil rigs?
Oil rigs typically use diesel engines and generators to provide the necessary power for various drilling operations.